How Is Glass Manufactured?
Glass surrounds us in our daily lives, from the windows we look through to the screens we interact with, yet many of us rarely consider the fascinating process behind its creation. This transparent material that we often take for granted has a rich history and complex manufacturing process that combines ancient techniques with modern technology. Wondering how is glass manufactured? In this comprehensive guide, we’ll explore everything behind glass manufacturing.
What is Glass?
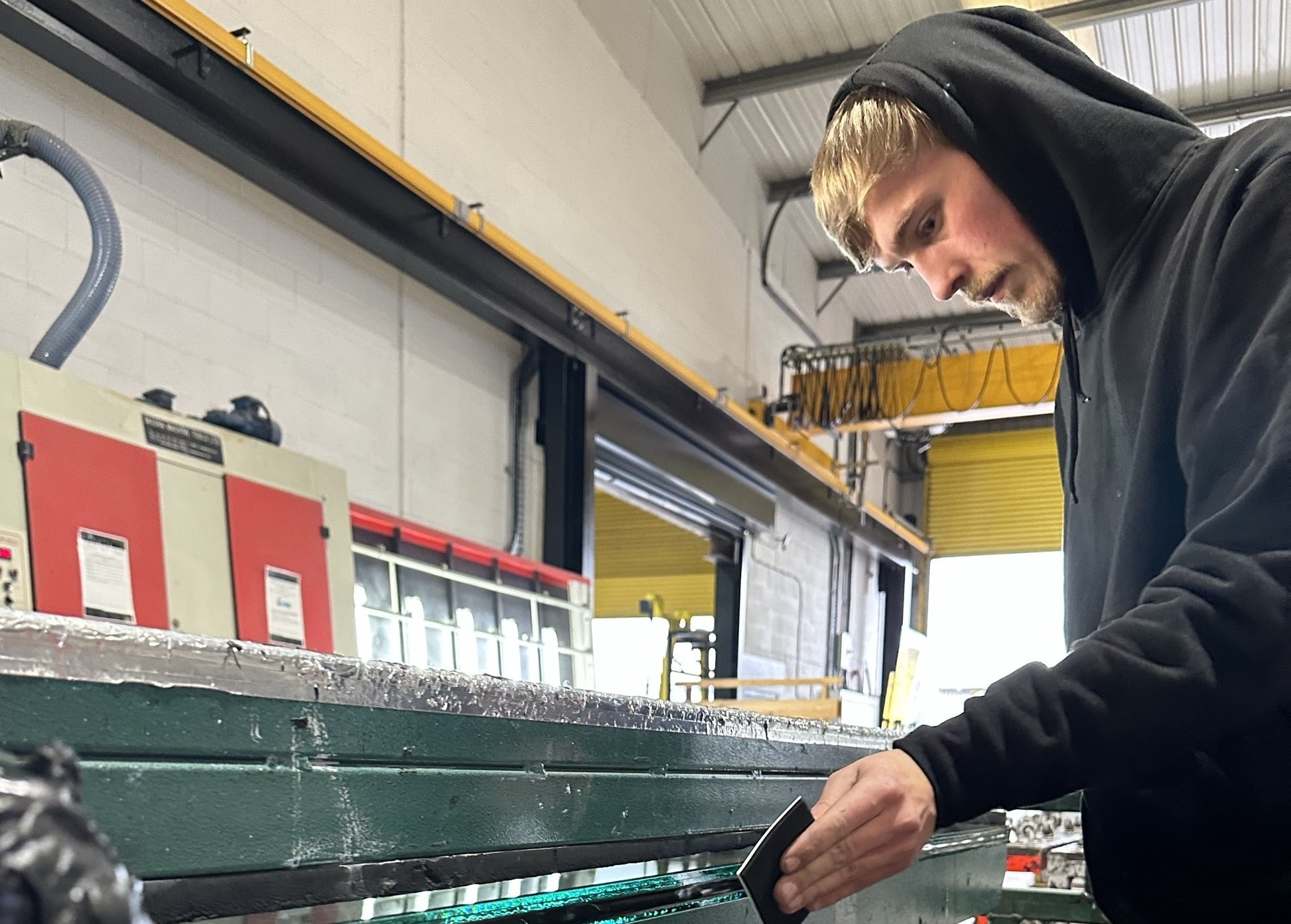
Glass is a versatile and widely used material made from a mixture of raw materials. These materials often include silica sand, soda ash, limestone, and dolomite. The process of making glass involves heating these raw materials to extremely high temperatures, typically around 1500°C, until they melt and form molten glass. This molten glass is then cooled and formed into the desired shape, resulting in a wide range of glass products, including windows, mirrors, lightbulbs, and containers.
One of the most fascinating aspects of glass is that it is an amorphous solid, meaning it lacks a fixed atomic structure. This unique property allows glass to be molded and shaped into various forms, making it a highly versatile material.
The Basic Components of Glass: How Is Glass Manufactured?
Glass manufacturing begins with carefully selected raw materials. At its most fundamental level, glass consists primarily of silica, which is typically sourced from sand. Manufacturers seek out high-quality silica sand with minimal impurities, particularly iron, which can give glass an unwanted greenish tint.
The primary ingredient, silica sand, typically makes up about 70-74% of the glass composition. This sand contains silicon dioxide (SiO₂), which forms the main structural network of the glass. To this foundation, glassmakers add several other crucial components that modify the properties of the final product.
Soda ash (sodium carbonate) serves as a flux in the mixture. This lowers the melting temperature of silica from an impractical 1700°C to a more manageable 1500°C. This reduction in temperature makes commercial glass production economically viable but introduces a significant drawback—the resulting glass would be water-soluble without additional ingredients.
To counter this solubility issue, limestone (calcium carbonate) is added to the batch. When heated, limestone releases carbon dioxide and transforms into calcium oxide. This acts as a stabiliser, making the glass resistant to water and enhancing its durability. This three-part mixture of silica, soda, and lime forms what we commonly call soda-lime glass, or more specifically, soda lime silica glass, which accounts for approximately 90% of all manufactured glass worldwide.
Depending on the intended application, manufacturers may incorporate various additional materials to impart specific properties.
Glass Manufacturing: The Melting Process
The transformation of raw materials into molten glass begins in the batch house. This is where ingredients are precisely weighed and thoroughly mixed according to specific formulations. This carefully prepared mixture, called the batch, is then transported to the furnace for melting.
Modern glass furnaces are designed to operate continuously for years without shutdown. These massive structures, often larger than a house, maintain temperatures between 1400°C and 1600°C using natural gas, oil, or electricity as fuel sources. The most common design is the regenerative furnace, which incorporates heat recovery systems to improve energy efficiency by preheating incoming combustion air using waste heat from exhaust gases.
Inside the furnace, the batch materials undergo several physical and chemical transformations. First, the materials heat up and release gases as carbonates decompose. As temperature rises, sand melts, transforming from into a liquid state, essential for forming the glass silicate network. The remaining materials then begin to melt, with silica being the last component to dissolve into the increasingly homogeneous mixture. Chemical reactions occur throughout this process, forming the silicate network that gives glass its unique properties.
The molten glass moves through the furnace in a carefully controlled flow pattern, spending approximately 24-48 hours in the melting environment. This time allows for the removal of bubbles (known as fining) and ensures thermal homogeneity throughout the glass mass. Mechanical stirrers or bubbling systems may be employed to enhance this homogenisation process.
Temperature control is absolutely critical during melting. Too low a temperature results in incomplete melting and poor quality, while excessive heat wastes energy and accelerates furnace deterioration. Advanced monitoring systems continuously measure temperature at multiple points throughout the furnace. Through this, operators can make precise adjustments to maintain optimal conditions.
Glass Production: Shaping Molten Glass
Once the glass has been properly melted and refined, it must be formed into useful products while still in a workable state. The temperature at which glass transitions from a molten liquid to a solid is not a distinct point but rather a range, allowing glassmakers to manipulate the material through various forming techniques.
Float glass production, the dominant method for manufacturing flat glass, was revolutionary when introduced by Pilkington in 1959. In this process, molten glass flows from the furnace onto a bed of molten tin in a controlled atmosphere. The glass naturally spreads out, forming a perfectly flat ribbon with uniform thickness. As it moves along the tin bath, the glass gradually cools until it’s rigid enough to be lifted onto rollers without marring the surface. This method produces the pristine flat glass used in windows, mirrors, and architectural applications.
Container glass formation employs either press-and-blow or blow-and-blow processes. In modern facilities, gobs of molten glass are cut to precise weights and delivered to forming machines, where they’re shaped into bottles, jars, and other containers. These processes are crucial for producing high-quality glass containers, such as bottles and jars, which must meet stringent quality standards. The press-and-blow method uses a metal plunger to create the initial cavity before air pressure inflates the container to its final shape. The blow-and-blow technique uses air pressure for both the preliminary and final shaping, offering advantages for certain container designs. Ensuring the quality of each glass product is essential, as defects can significantly affect their performance and safety.
The Cooling Phase
Wondering how is glass manufactured during the cooling phase? After forming, glass products must undergo a carefully controlled cooling process called annealing to ensure their structural integrity. When glass cools too quickly, different parts of the object cool at different rates, creating internal stresses that can lead to spontaneous breakage immediately or weeks later. Annealing relieves these stresses by holding the glass at a specific temperature—just below its softening point—for a period of time before gradually cooling it to room temperature.
The annealing process takes place in specialised kilns or lehrs, which are essentially long, temperature-controlled tunnels. Glass products enter the lehr at the hot end and move slowly through progressively cooler zones. The specific temperature profile and transit time depend on the glass composition and the thickness of the product being annealed.
Modern annealing operations use sophisticated computer controls to maintain precise temperature profiles throughout the lehr. Temperature sensors monitor conditions at multiple points, and automated systems adjust heating elements to maintain the ideal cooling curve. This precision ensures consistent quality while optimising energy usage.
Secondary Processing and Finishing
Most glass products require additional processing after annealing to prepare them for their intended applications. These secondary operations transform basic glass forms into finished products with specific properties and appearances.
From cutting to custom sandblasting, we offer a comprehensive range of in-house services to ensure every piece of glass is manufactured to the highest standard. Whether you’re after toughened safety glass, oversized units, or decorative finishes, UKO Glass combines cutting-edge technology with expert craftsmanship to bring your glass vision to life. To find out more, or to place an order today, drop us an email on info@ukoglass.co.uk.